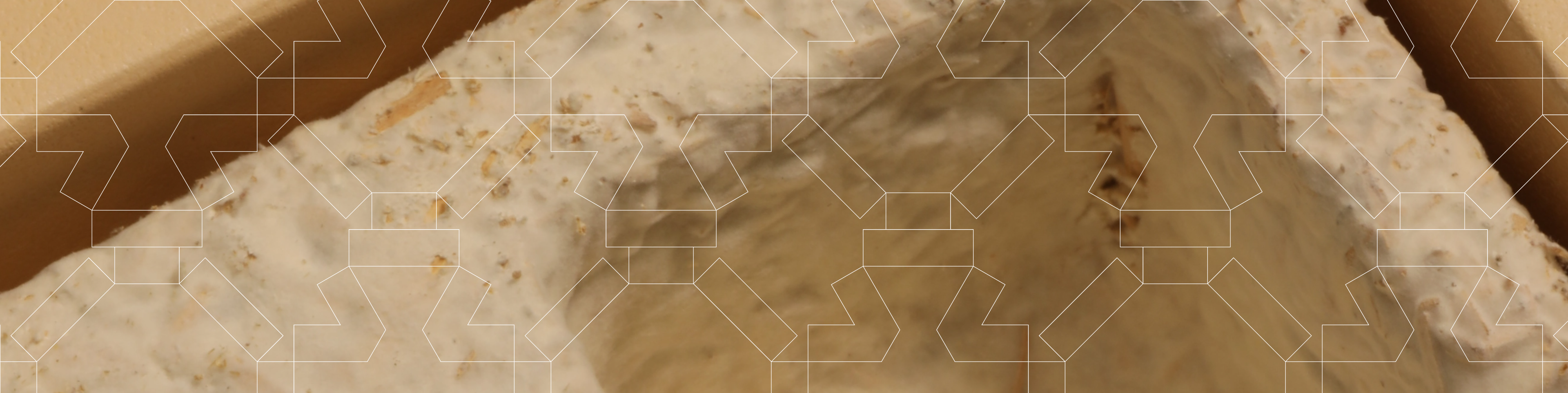
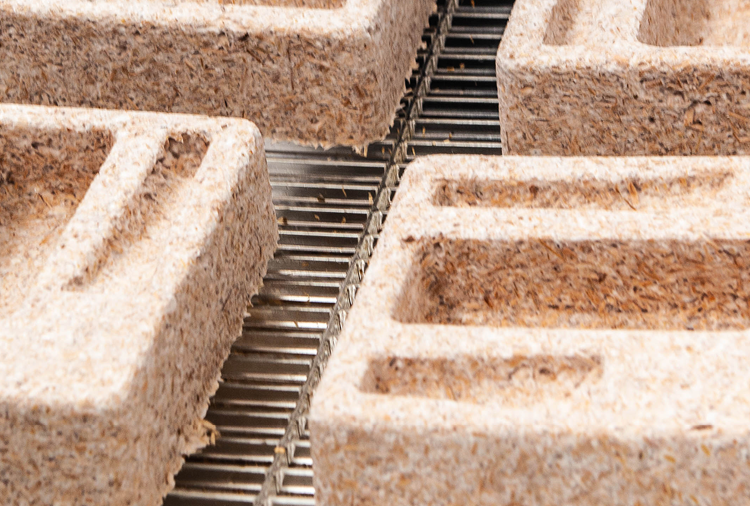
Our Process
Our packaging is grown, not manufactured.
We offer a high-performing, cost competitive packaging solution which is naturally thermally insulating and water resistant. Mushroom® Packaging grows in 7 days using mycelium, the roots of mushrooms, as the biological binder, and is fully home-compostable in 45 days.
Once we’ve identified the opportunity fit, we’ll look to connect you with the appropriate Mushroom® Packaging licensee for your region.
Mushroom® Packaging is

CAD
1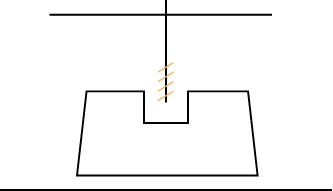
CNC Milling
2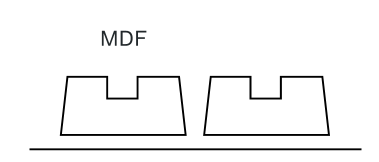
Hard Tooling
3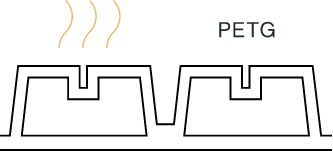
Thermoform Growth Trays
4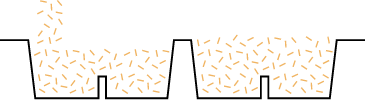
Fill Parts with Hemp & Mycelium
5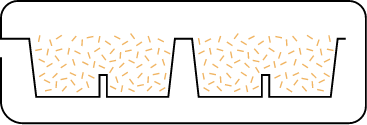
Internal Growth in Pod
6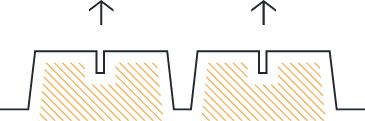
Pop Parts
7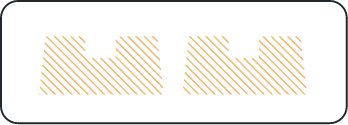
External Growth in Pod
8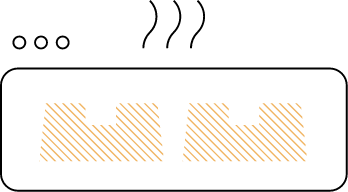
Dry Parts
9Our process. Step by step.
Our designers generate a 3D model of your Mushroom®Packaging insert and route a positive using a CNC machine.
We thermoform the positive to make growth trays — which are reused numerous of times.
The trays are filled with our hemp hurd and mycelium blend which grow for 4 days.
The grown parts are removed from the tray and continue to grow for 2 more days to create a velvety layer of overgrowth.
The parts are dried to disable future growth. The Mushroom® Packaging is ready to protect your product in shipment.
Custom Design Timeline
Phases and lead times for the Mushroom® Packaging
Custom Design Process & OverviewCustom Design Timeline
Phases and lead times for the Mushroom® Packaging
Dimension Drawing + Render
1-2 business days per iteration
Custom Grown Prototype
3-4 weeks per iteration
Quote + PO
1 week
Includes production tooling costs and per-piece price.
Tooling + Pilot Run
3–4 weeks
Production
6–12 weeks
Lead time varies by licenses, annual volume needs and tooling investment.
Design Constraints
Guidelines and Considerations for Mushroom® Packaging
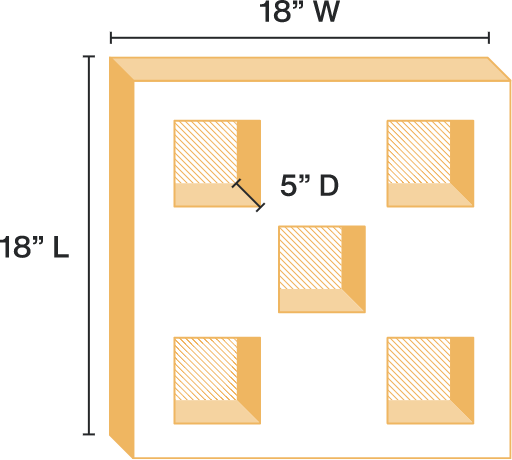
Maximum Part Dimensions:
18 x 18 x 5”
Smaller parts fit multiple per tray.
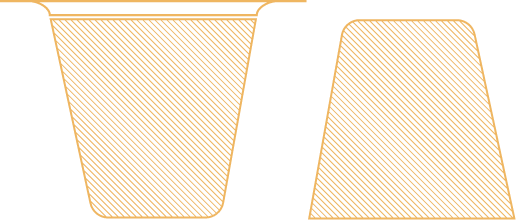
Fill surface
After Popping
Fill Surface + Flash
Every tray is filled in one direction, typically on the bottom because it is flat. The fill surface texture is rougher than the molded surface.
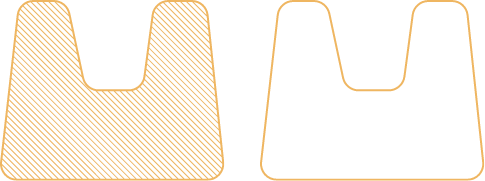
Velvety Overgrowth
4 days in tray (internal growth)
2 days no tray (external growth/ overgrowth)
1 day to dry, preventing further growth and fruit mushrooms.
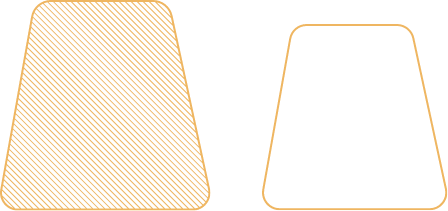
Contraction
Parts must be scaled up since they shrink when drying:
4% in the x axis
4% in the y axis
7% in the z axis
Incorrect
Correct
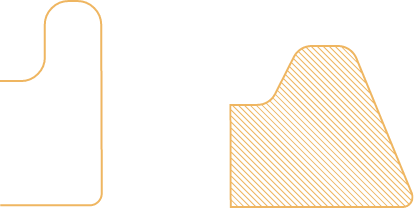
Draft Angles
At least a 3 degree draft angle on all vertical walls, with no undercuts
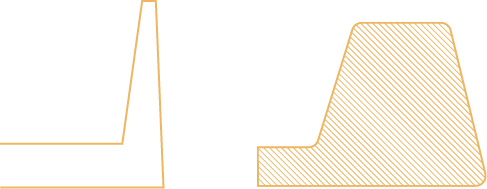
Wall Thickness
Minimum of ⅜” to to avoid voids. Avoid large, thin walls which can warp and are structurally weak.
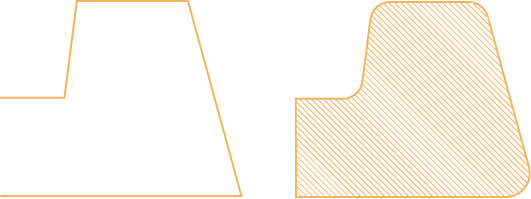
Edges
Fillet all edges with a minimum radius of 0.125”
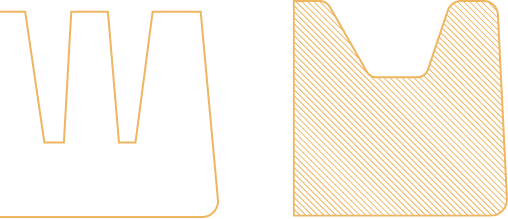
Draw Ratio
The draw ratio should be at least 1 unit wide by 1 unit tall. Avoid deep cavities.
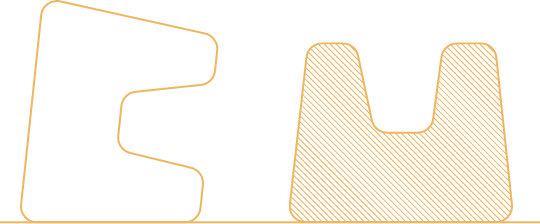
Orientation
Standing upright on shelves is not recommended due to draft angles. Product will tilt downward and could fall.